How to Recognize What is Porosity in Welding and Improve Your Technique
Wiki Article
Porosity in Welding: Identifying Common Issues and Implementing Best Practices for Prevention
Porosity in welding is a prevalent problem that typically goes unnoticed until it triggers considerable issues with the integrity of welds. In this conversation, we will certainly explore the key elements contributing to porosity formation, analyze its damaging impacts on weld performance, and review the ideal methods that can be adopted to decrease porosity event in welding processes.Common Reasons of Porosity

Utilizing filthy or damp filler materials can present pollutants into the weld, contributing to porosity concerns. To minimize these common causes of porosity, detailed cleaning of base steels, correct securing gas option, and adherence to ideal welding parameters are vital practices in attaining high-quality, porosity-free welds.
Impact of Porosity on Weld Quality

The existence of porosity in welding can dramatically compromise the structural integrity and mechanical residential properties of welded joints. Porosity develops gaps within the weld steel, deteriorating its total stamina and load-bearing capability.
Welds with high porosity degrees often tend to display reduced influence toughness and reduced capability to warp plastically prior to fracturing. Porosity can hamper the weld's capacity to properly transfer pressures, leading to early weld failure and prospective safety hazards in important structures.
Ideal Practices for Porosity Avoidance
To enhance the structural integrity and high quality of bonded joints, what particular steps can be applied to decrease the event of porosity throughout the welding process? Using the appropriate welding technique for the specific product being welded, such as readjusting the welding angle and gun setting, view it can additionally avoid porosity. Normal examination of welds and instant removal of any problems determined his response during the welding procedure are essential methods to stop porosity and generate premium welds.Relevance of Correct Welding Strategies
Implementing correct welding strategies is critical in making sure the architectural integrity and quality of bonded joints, building on the structure of reliable porosity prevention actions. Welding strategies straight impact the overall stamina and resilience of the welded structure. One vital facet of appropriate welding techniques is preserving the appropriate heat input. Too much warm can bring about increased porosity as a result of the entrapment of gases in the weld swimming pool. Conversely, not enough heat may result in incomplete combination, producing possible powerlessness in the joint. In addition, using the suitable welding parameters, such as voltage, present, and travel rate, is critical for accomplishing audio welds with marginal porosity.Additionally, the selection of welding procedure, whether it be MIG, TIG, or stick welding, ought to align with the details needs of the task to make certain optimum results. Proper cleaning and preparation of the base metal, in addition to selecting the ideal filler material, are additionally essential components of efficient welding strategies. By sticking to these best practices, welders can lessen the risk of porosity formation and create premium, structurally audio welds.
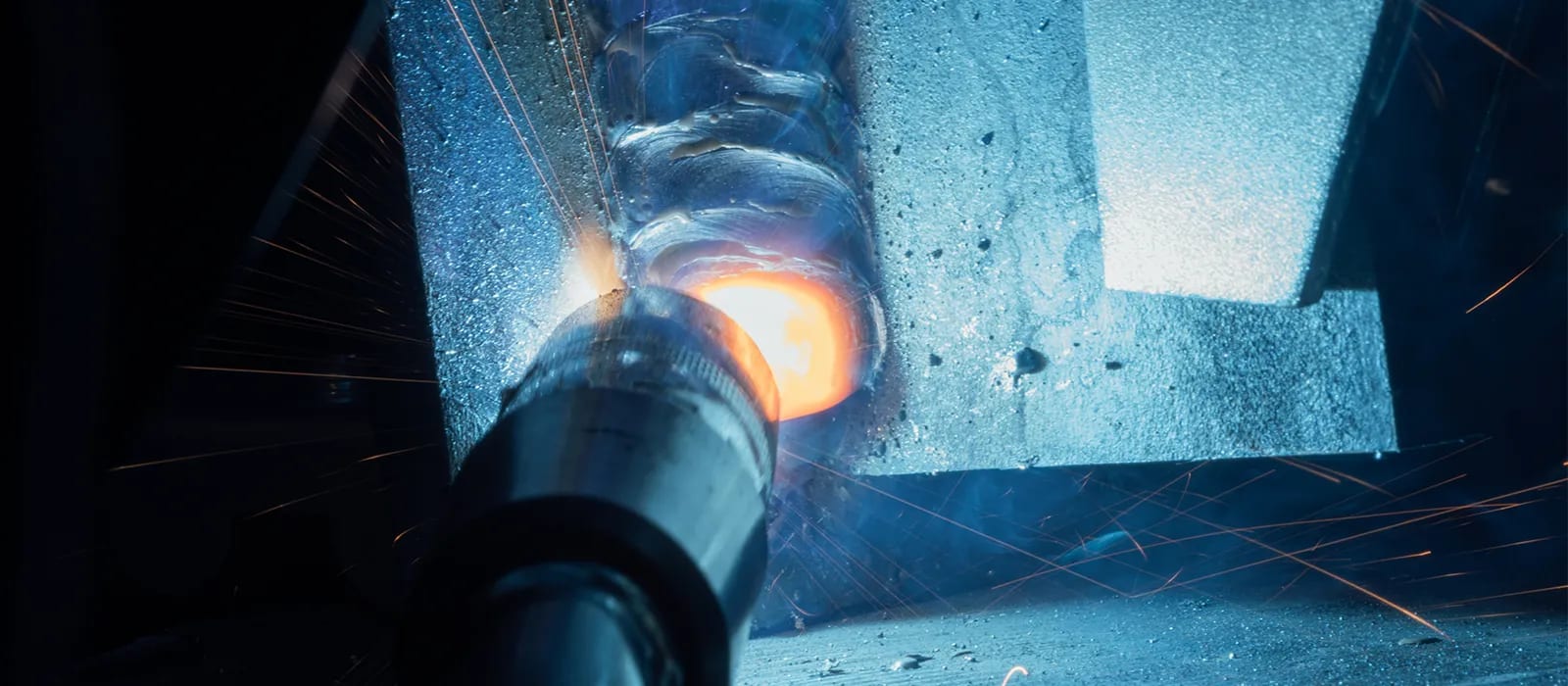
Checking and Quality Assurance Measures
Examining procedures are crucial to spot and prevent porosity in welding, making certain the toughness and longevity of the final product. Non-destructive screening techniques such as ultrasonic Discover More testing, radiographic screening, and visual examination are typically employed to determine prospective flaws like porosity.Post-weld evaluations, on the various other hand, examine the last weld for any kind of problems, including porosity, and confirm that it fulfills specified standards. Executing a thorough top quality control plan that includes detailed screening treatments and evaluations is extremely important to minimizing porosity concerns and guaranteeing the general high quality of welded joints.
Conclusion
To conclude, porosity in welding can be an usual problem that impacts the quality of welds. By identifying the common causes of porosity and carrying out ideal techniques for prevention, such as correct welding techniques and screening actions, welders can ensure premium quality and reputable welds. It is vital to focus on avoidance methods to reduce the incident of porosity and keep the honesty of bonded frameworks.Report this wiki page